The Importance of Keeping Your Equipment Up To Date
Stay Ahead of the Curve: Why Updating Your Equipment Matters
Equipment is what keeps your business running day after day. Do you know how close to obsolescence your company’s equipment is? If you don’t plan for upgrades and replacements before reaching obsolescence, you’re risking breakdowns, delays, and higher costs. Delaying a new equipment purchase might save money in the short-term, but there are potential consequences to consider. In this article, we’ll explain what equipment obsolescence is, the different ways equipment can become obsolete, and how to plan for upgrades.
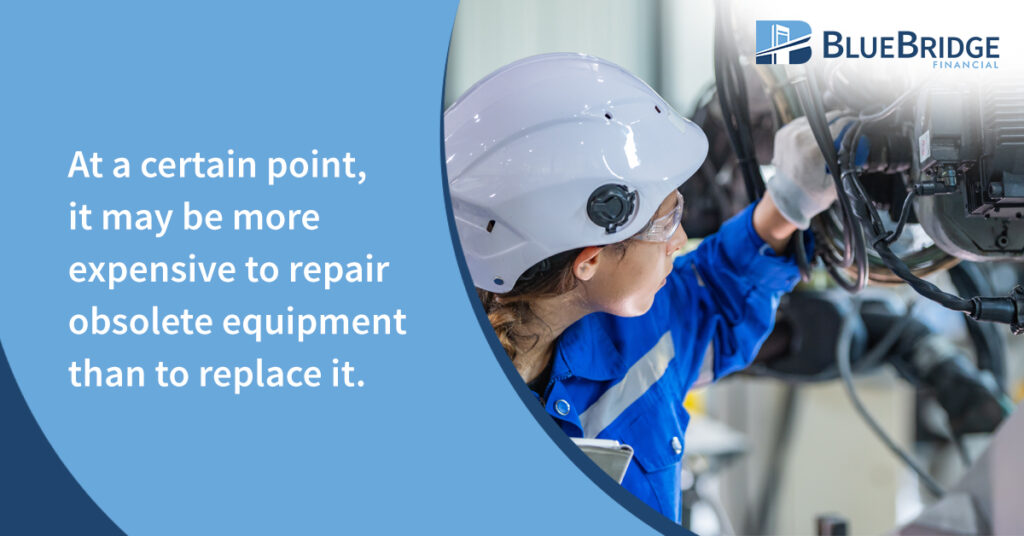
What is Equipment Obsolescence?
Obsolescence is an inevitable part of the equipment life cycle. Understand the different reasons for equipment obsolescence so you can manage it.
Natural Deterioration
Vehicles, heavy machinery, and other equipment naturally declines in functionality over time. Lack of maintenance and improper use of equipment can speed up the deterioration process.
At a certain point, it may be more expensive to repair older equipment than to replace it. If you don’t keep track of your equipment’s lifespan and maintenance schedule, you may end up dealing with unexpected downtime and other disruptions. Avoid the costs of losing or delaying work by planning ahead with an equipment audit.
Performing an equipment audit means collecting information on when each piece of equipment was made, how long it’s been in use, the number of service visits or repairs, and whether replacement parts are still available. Use this data, along with the original manufacturer’s projected life expectancy, to track how much time is left before the equipment will be obsolete.
Manufacturer Planned Obsolescence
Manufacturers often plan on their products becoming obsolete every few years. This is a way to continue generating income by forcing customers to purchase a new model instead of repairing what they have. Planned obsolescence usually happens through updated designs and features, discontinued spare parts, and use of non-durable materials. For example, think of your cell phone or laptop computer. At a certain point, these mobile devices can no longer receive software updates. Battery life declines and the device may run more slowly.
You can stay ahead of planned obsolescence by accounting for the cost of upgrades in your budget. For example, if you need equipment financing to replace an obsolete item, we’ll work with your budget to get you affordable monthly payments.
Technological Obsolescence
This is when technology advances enough to render your current equipment no longer useful. You find you need to upgrade to stay competitive. Just as computer and car models have been rendered obsolete over the years by technological advancements, construction and other commercial equipment can also become obsolete through technology.
On the plus side, investing in new, technologically advanced equipment can lead to more efficiency and less equipment downtime. Sometimes the size of a piece of equipment shrinks with each update and then you can fit more equipment in the same space.
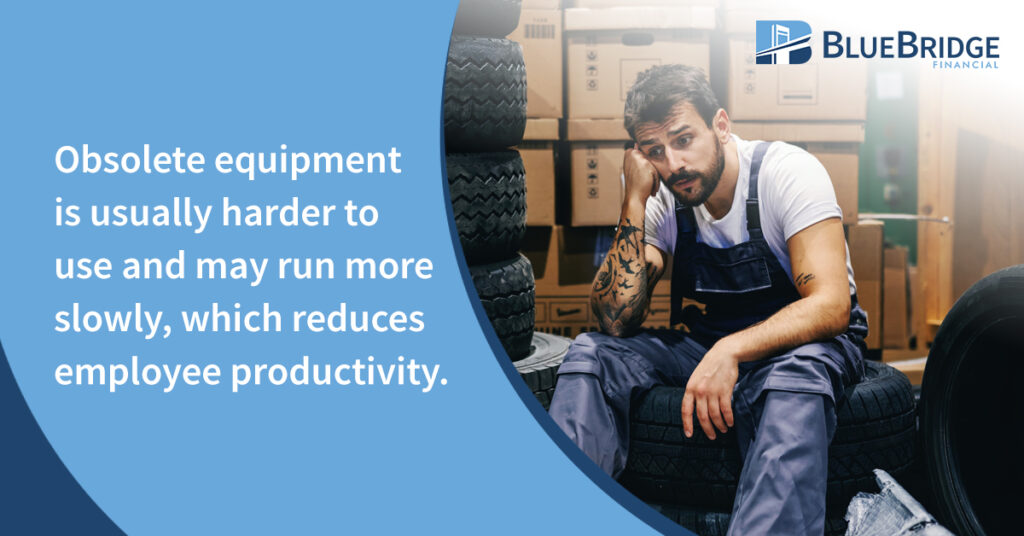
4 Risks of Using Obsolete Equipment
It’s always tempting to save money by delaying a large equipment purchase. However, waiting until the last possible minute to replace obsolete equipment can end up being more costly in the end. Here are the 4 biggest risks you run by continuing to use obsolete equipment.
- Downtime and delays: If a critical piece of equipment suddenly stops working, your production could grind to a halt or a client project could be delayed, damaging your reputation.
- Reduced Productivity: Obsolete equipment is usually harder to use and may run more slowly, which reduces employee productivity. Morale may be lower, too, from the frustration of using old or half-broken equipment.
- Larger operating costs: When you try to repair an older piece of equipment, you may find that parts are more expensive because you can’t just order it from the manufacturer. Instead, you have to compete with other business owners to find available used or off-market parts.
- Cybersecurity threats: When it comes to using obsolete technology such as computers, smartphones, and tablets, you run the risk of cybersecurity threats. Older and un-updated systems are easier for hackers to penetrate.
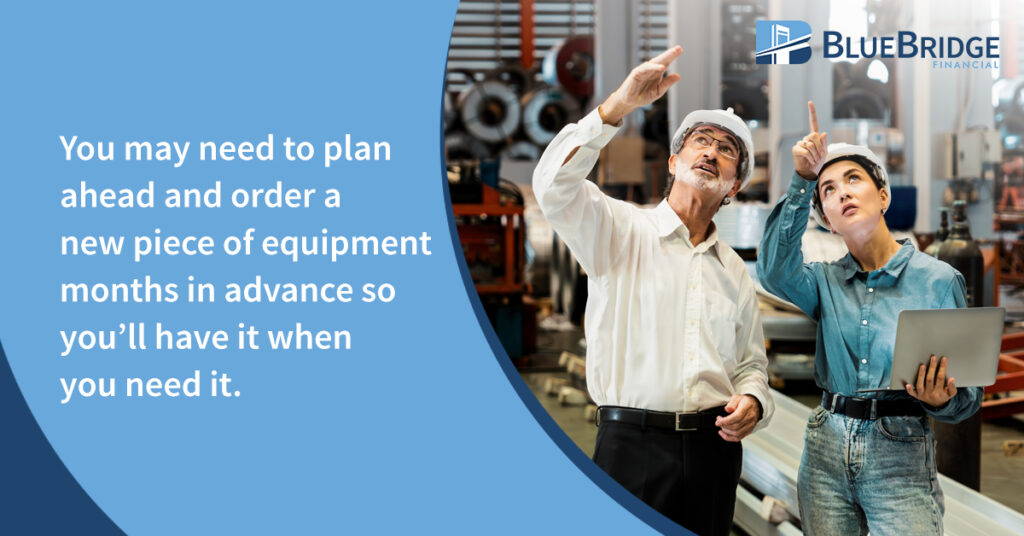
How To Plan Your Equipment Upgrade
Of course, you can’t just upgrade equipment on a whim. It’s best to plan for equipment upgrades so you can minimize business downtime and control costs. Talk to stakeholders at your company and get feedback from the employees who use this equipment. They are best-positioned to know which features are useful or not, and which are nice-to-haves but not essential.
Next, consider whether you can make upgrades in phases. Does everything need to be replaced at the same time or can you spread it out? Keep in mind that many manufacturers are still experiencing production delays.
Finally, think about how accounting strategies like depreciation and equipment financing options like an EFA (with little to no down payment) can make your equipment upgrades more affordable.
About Blue Bridge Financial
Blue Bridge Financial is your experienced equipment lender for all types of businesses nationwide. We can help you finance your next equipment purchase with loan payments that fit your budget and maintain your cash flow. Contact us to learn more about our equipment financing options and start the application process.
Any Questions? We'd Love to Talk:
About the Author
Nick Devernis is the Vice President of Business Development with expertise in credit analysis and equipment financing. With over 6 years in equipment financing, he offers a wealth of knowledge to readers of Blue Bridge Financial’s blog. He currently oversees the California office and leads the Sales and Marketing departments. Nick’s role as Vice President of Business Development involves management of the sales team, relationship management, and developing strategic partnerships to drive inbound and outbound originations.p> LinkedIn Profile